Inside the Compressed Mattress Production Process
The Journey Begins: Material Selection
The creation of a compressed mattress starts with the careful selection of materials. Manufacturers typically use a combination of memory foam, latex, and high-density foam to ensure comfort and durability. These materials are chosen for their ability to conform to the body while providing support.
Each type of foam has its own unique properties. For instance, memory foam is celebrated for its pressure-relieving qualities, while latex offers a more responsive and bouncy feel. High-density foam contributes to the mattress's longevity and structural integrity.
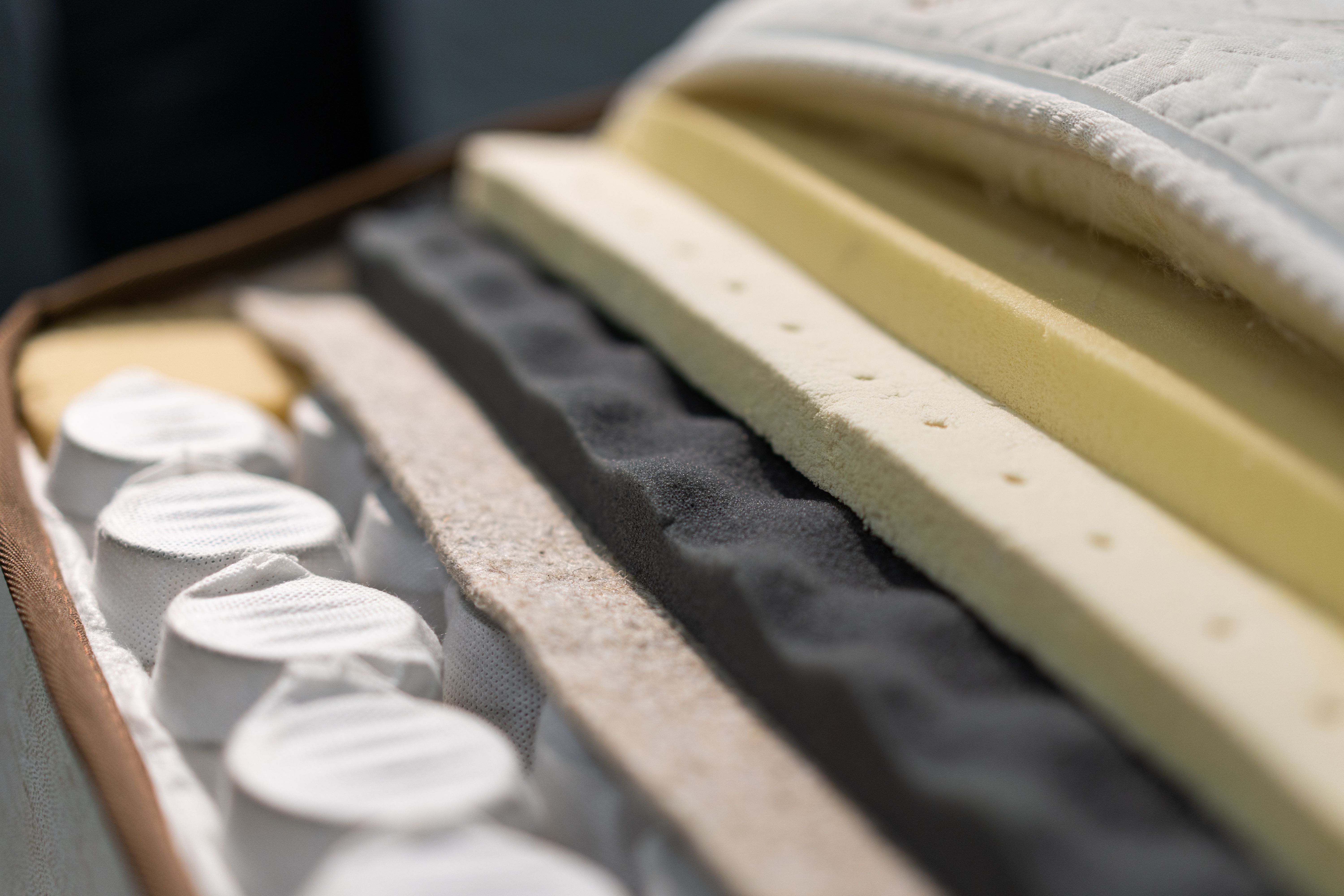
Precision Cutting and Layering
Once the materials are selected, the production process moves to precision cutting and layering. Advanced machinery cuts the foam into specific dimensions required for different mattress sizes. This step is critical to ensure that each layer fits perfectly within the overall design.
After cutting, these layers are meticulously stacked in a predetermined sequence. The layering process plays a significant role in determining the mattress's firmness level and overall comfort. Manufacturers often experiment with different configurations to cater to diverse sleep preferences.
Compression and Packaging
The next step in the production process is compression. Using state-of-the-art technology, mattresses are compressed to a fraction of their original size. This not only makes them easier to transport but also reduces shipping costs and environmental impact.
After compression, the mattress is rolled and sealed in airtight packaging. This packaging is designed to maintain the integrity of the mattress during transit. A vacuum-sealing process helps in retaining the compressed state until the mattress is ready to be unpacked by the consumer.
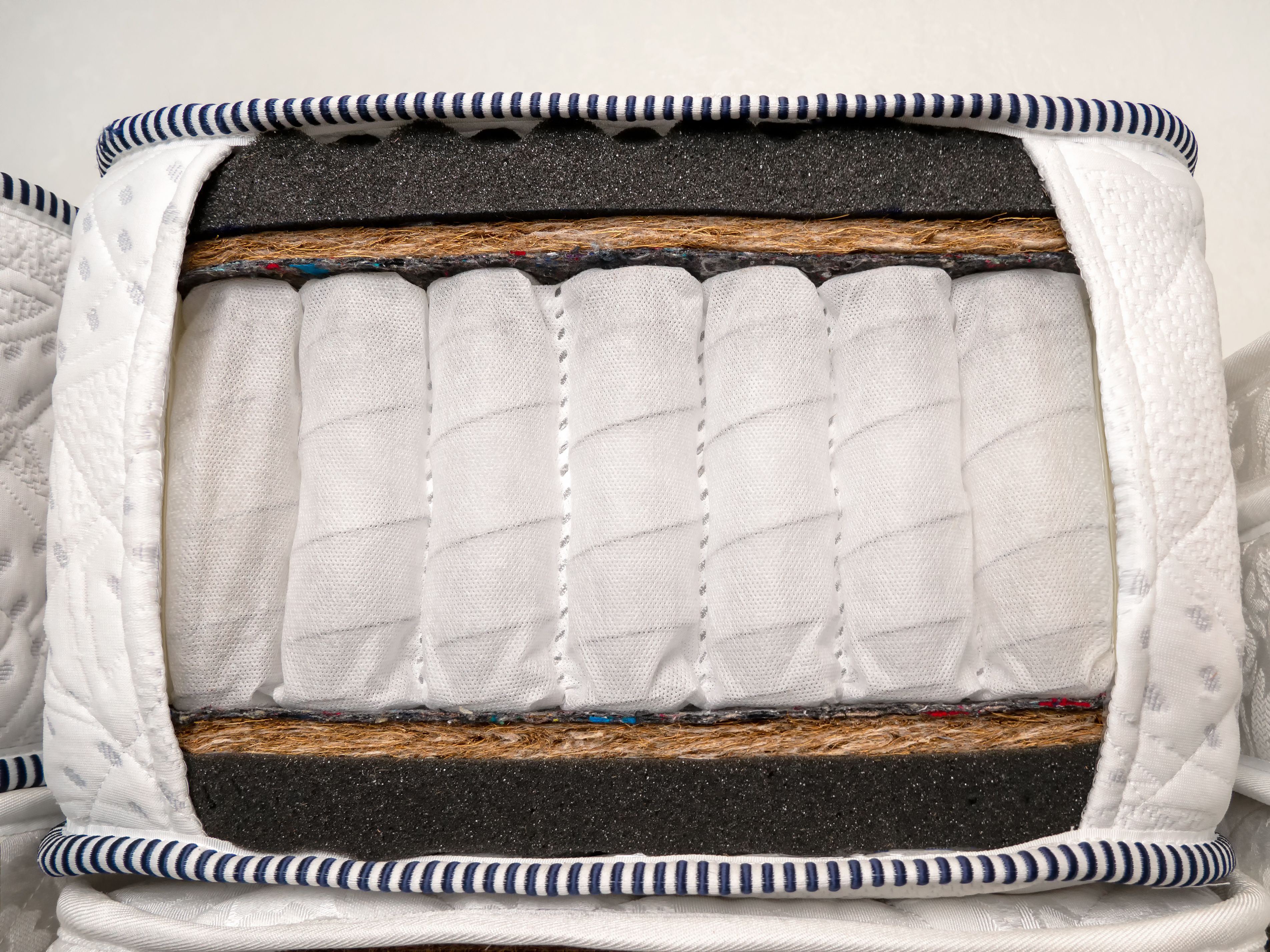
Quality Assurance and Testing
Quality assurance is an integral part of the compressed mattress production process. Each mattress undergoes rigorous testing to ensure it meets industry standards for durability, support, and safety. These tests simulate years of use in a short period, helping manufacturers guarantee long-term performance.
Manufacturers often employ third-party testing agencies for an unbiased evaluation. This step assures customers of the product's quality and reliability, fostering trust and customer satisfaction.
The Final Touch: Branding and Shipping
Once the mattresses pass all quality checks, they are ready for branding and shipping. Manufacturers add labels, care instructions, and branding elements to each unit. This step is crucial for brand recognition and providing essential information to the consumer.
The final product is then boxed and prepared for shipment. Many companies offer direct shipping to customers' homes, eliminating the need for physical retail stores. This direct-to-consumer model has revolutionized the mattress industry, making high-quality mattresses more accessible than ever before.
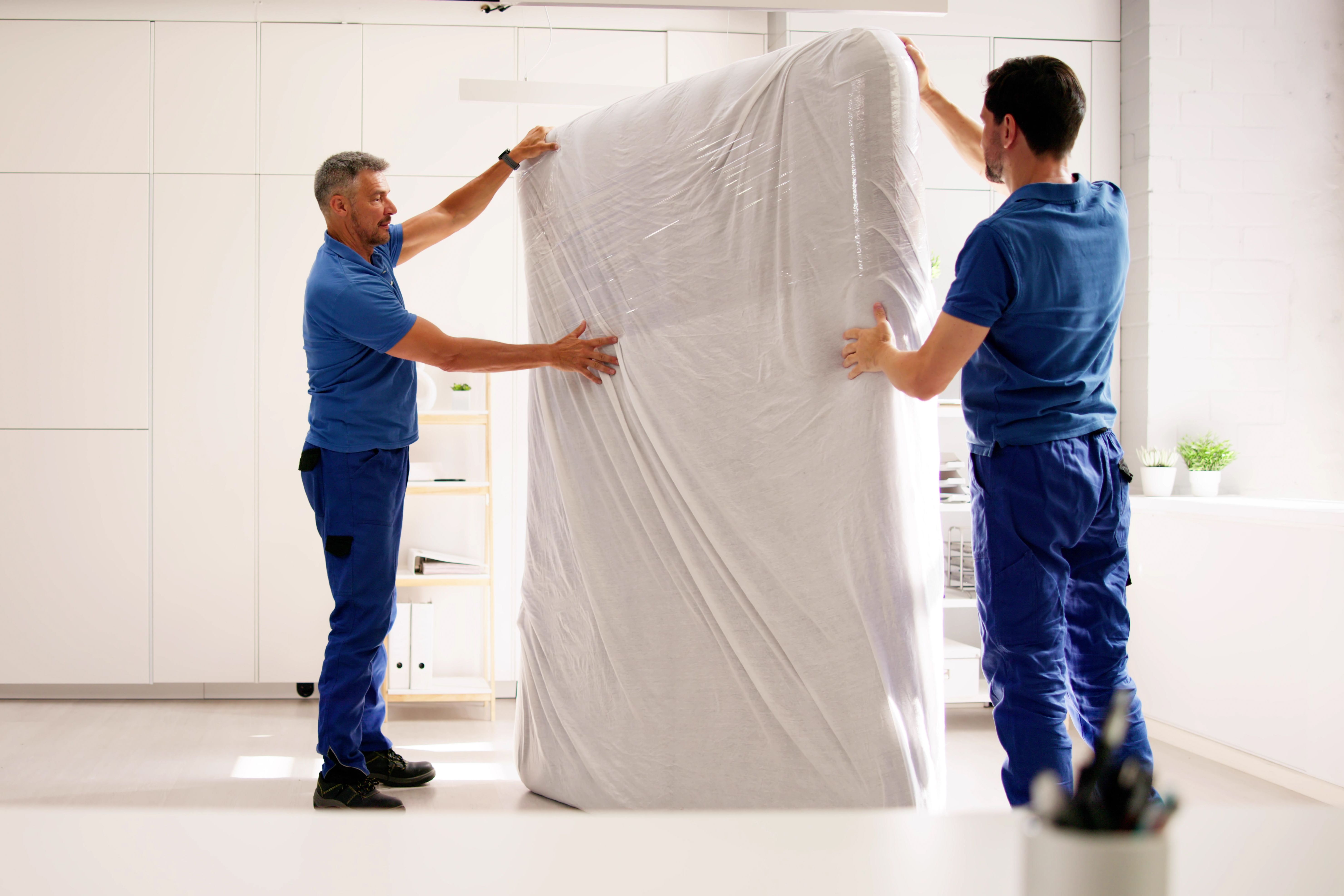
The Unboxing Experience
For consumers, the unboxing experience is both exciting and convenient. Upon delivery, customers can easily unpack their new mattress by removing it from its box and allowing it to expand to its full size. Most mattresses reach their intended shape within a few hours.
This hassle-free setup process is one of the main attractions of compressed mattresses, offering a blend of convenience and innovation that aligns with modern lifestyles.